Summary
- For supply chain and logistics operations professionals, receiving of packages, pallets, and containers at the warehouse is inefficient because of manual processes, a lack of digitization, and disconnected inventory workflows.
- Adding automation to inbound receiving processes can help improve downstream workflows by digitizing data from labels at the start, expediting inspection and sorting times, and maximizing warehouse efficiency.
- PackageX Receive and PackageX Inventory empower workers to digitize data from inbound labels using AI-powered optical character recognition (OCR) technology.
Warehouse management is a notoriously difficult element of the supply chain to get right. Not only do businesses have to organize and coordinate complex logistics, they also have to contend with persistently rising warehouse storage costs.
According to commercial real-estate services firm Cushman & Wakefield, rents from 2022 to 2023 grew 10% YOY, even as warehouse availability surged to the highest levels since the pandemic. With rents now at $9.79 per square foot, companies must explore new warehousing and inventory strategies to lower costs, improve product flows, and enhance operational efficiency.
However, a recent study on warehouse management found that “every measurable process can be optimized by different optimization approaches and methods.” This includes the warehouse receiving process, which can be streamlined, optimized, and automated to remove bottlenecks and improve efficiency.
In this article, we’ll explain what you need to know about mastering warehouse receiving operations. In addition to covering the key steps, benefits, and metrics to track, we’ll highlight some of the most important strategies you can implement to improve inventory receiving processes, including how to use modern technologies to uplevel your operations.
Let’s begin!
What Is the Warehouse Receiving Process?
The warehouse receiving process involves all inbound operations for accepting, recording, and storing incoming inventory and shipments at a warehouse or fulfillment center. Some of the procedures and tasks include unloading and inspecting shipments, counting inventory, preparing documentation, and organizing and storing products within the warehouse.
The warehouse receiving process aims to ensure that incoming inventory is accurately accounted for, properly stored, and ready for downstream operations in the supply chain, such as picking, packing, and shipping.
The main steps in the warehouse receiving process
1. Pre-receive
For easy processing, proper documentation is required before inventory can be sent from a supplier or manufacturer to the receiving warehouse. Requirements generally include:
- Number of packages per pallet
- Packaging materials
- Packaging dimensions
- Weight limits
- Labeling requirements
- Packing instructions
- Special handling instructions
To ensure compliance with pre-receiving requirements, businesses may need to fill out Warehouse Receiving Order (WRO) labels and follow guidelines set by third-party logistics providers (3PLs).
2. Receive and unload
Warehouse workers receive incoming inventory in packages, pallets, and containers at the loading docks before unloading goods. Businesses need to allocate the right equipment for the size and quantity of the cargo and also allocate the right amount of warehouse staff for receiving stock. This can be done with scheduling software integrated with a warehouse management system (WMS).
Truck beds should be packed back-to-front in the reverse order of the delivery schedule so that warehouse workers can unload inventory quickly and efficiently. Warehouse workers should also check the integrity of seals, check temperatures (in case of perishables), and validate booking references when unloading.
3. Count and inspect
The next step is to cross check and verify that the received goods match the documentation. Received items are inspected for acceptable condition and accurate quantities.
One type of shipping and receiving software that can be used is inventory management software for scanning labels, extracting package/item data, matching inbound shipments against inventory, and updating stock levels. The use of smartphone barcode scanners and radio frequency identification (RFID) integrated to a WMS helps to speed up counting and minimize errors. Data can also be extracted from a bill of lading (BOL) using optical character recognition (OCR) technology. The identification of goods may include:
- Product name
- Manufacturer’s name
- Production date
- Expiry date
- Serial number
- Batch
- Quantity of stock
- Product quality
- Country of origin
4. Putaway and store
Putaway is the movement of goods from the receiving dock to the storage locations in the warehouse. Goods are sorted, organized, transported, and stored on a pallet, shelf, or bin, depending on the size and quantity of products.
An efficient putaway system optimizes transport time and distance, storage capacity and availability, and prioritizes employee safety. Goods are organized using ABC analysis for easy retrieval and distribution. Stock is rotated usually based on a first-in first-out (FIFO) or last-in first-out (LIFO) basis. Some widely used storage methods include floor/block stacking for products in unit loads, pallet flow rack for fast moving product using FIFO, push back racks are best used for LIFO, and mezzanine flooring and use of containers.
Key Benefits of Modernizing Warehouse Receiving
Can modern technologies be used to optimize the entire warehouse receiving workflow? Across receiving, putaway, and storage, many benefits can be realized. For example, businesses can automate manual processes, gain better inventory visibility, maximize warehouse space utilization, reduce safety stock, minimize out-of-stock situations, lower costs, and improve inventory turnover.
Automate manual processes
Spreadsheets and other forms of manual data entry lead to errors, delays, and bottlenecks. Inventory management automation in the receiving process increases accuracy, improves inventory availability and throughput, and bolsters scalability.
Gain real-time inventory visibility
By using inventory management software to scan labels and extract package/item data to match inbound shipments against inventory, businesses can log and track items in real time and gain better inventory visibility throughout the product life cycle.
Maximize warehouse space utilization
Empty warehouse space wastes resources, while overpacked warehouse space slows pick, pack, and ship operations. Achieving optimal storage utilization starts during the warehouse receiving process, where a WMS can digitize and log warehouse activity automatically, integrate with legacy systems, and organize and store inventory to optimize warehouse space.
Reduce the amount of safety stock and minimize out-of-stock situations
Safety stock is the extra inventory a company keeps on hand to mitigate the risk of stockouts. Using technology to modernize warehouse receiving increases inventory visibility and availability, lowering the need for safety stock.
Lower costs
By streamlining receiving operations, businesses can minimize labor hours, decrease error rates, and eliminate expenses related to inventory discrepancies or stockouts. Implementing technology-driven solutions simplifies inventory counting and inspection processes, making them less resource-intensive and more accurate.
Improve inventory turnover
Inventory management is a critical element of the warehouse receiving process. By tracking and managing the movement of goods, businesses can turnover more inventory faster and gain a complete chain of custody of goods for better accountability and security.
4 Must-Have Technologies to Supercharge Warehouse Receiving Processes
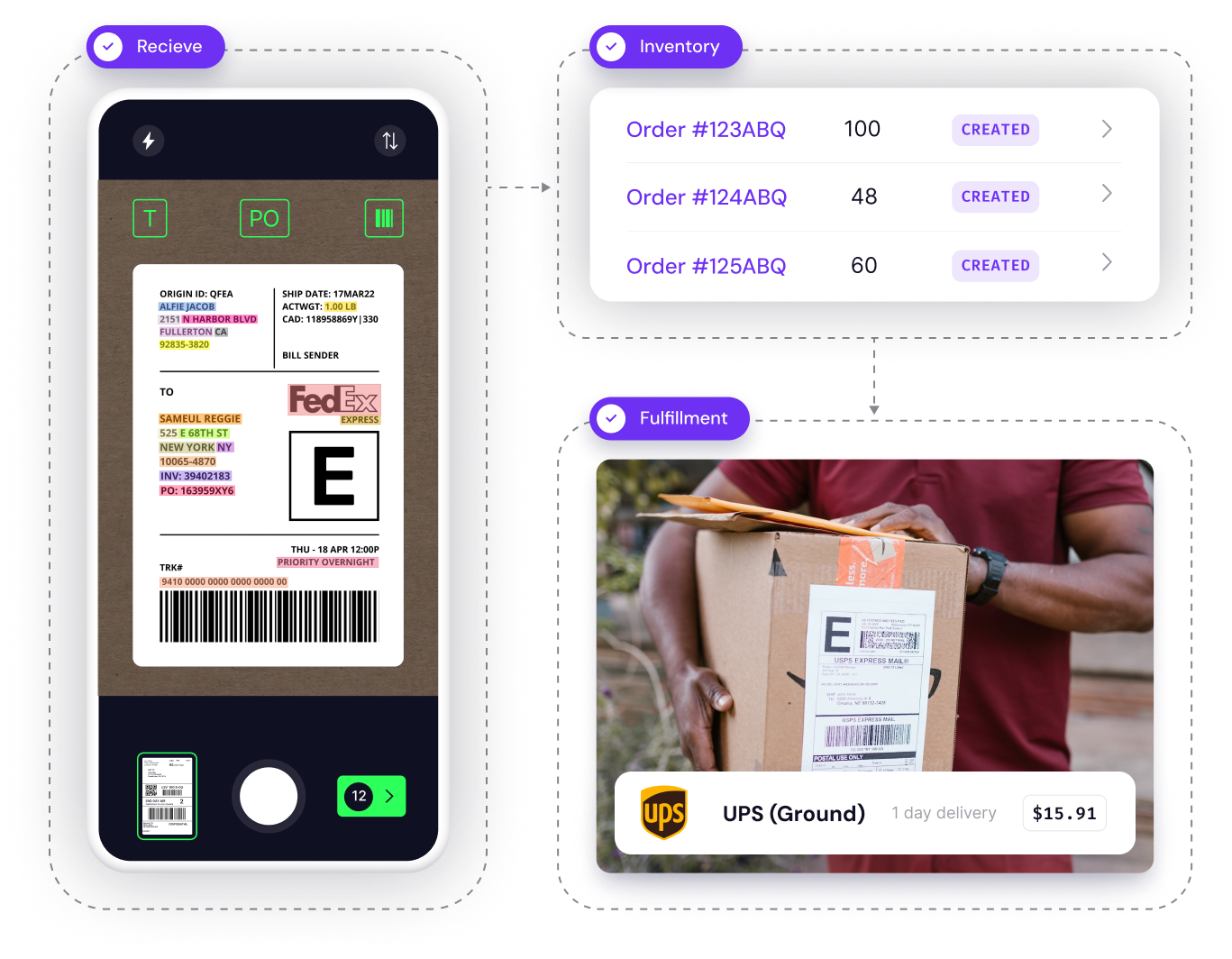
According to a recent study, 69% of warehouse decision-makers already have or are planning to automate workflows while 88% say that adding warehouse technologies attract and retain employees.
However, inaccurate inventory and out-of-stock situations continue to be a challenge. Businesses today require modern technologies to create smart warehouses that can optimize receiving, improve inventory accuracy and visibility, and ultimately enhance overall supply chain performance.
- Warehouse Management System (WMS)
Implementing a WMS enables automated tracking of incoming shipments, streamlining the receiving process from start to finish. For shipping and receiving improvements, WMS software can be used to automate tasks such as inventory verification, barcode scanning, and data entry.
- OCR, QR code, barcode, and RFID technologies
When receiving and unloading inbound inventory, OCR technology can be used to automate data extraction from various documents like shipping labels, bills of lading, and invoices. QR code and barcode inventory systems are critical for managing inbound inventory, tracking items, and ensuring the accuracy of inventory. Radio frequency identification (RFID) technology can also quickly and accurately capture product information during receiving. These technologies enable real-time tracking of inventory movements and reduce manual data entry errors.
By equipping warehouse staff with mobile devices such as smartphones or tablets loaded with receiving applications, workers can access real-time data, capture more product information, and update inventory records on the go.
- Inventory Management Software
Inventory management software is critical for optimizing warehouse receiving. It not only centralizes inventory data and provides real-time visibility into stock levels, orders, and shipments, it also allows businesses to monitor and control their inventory for faster and more efficient putaway and storage.
- Artificial intelligence (AI) for logistics
AI-powered label scanning is technology that utilizes the latest in machine and deep learning algorithms to empower warehouse workers to scan and extract data from any type of label.
For example, PackageX’s label scanning and BOL scanning technology boasts 95% scan accuracy and is trained by tens of millions of labels, price tags, license plates, and more. They use machine and deep learning algorithms to correct mistakes, improve accuracy, and drive efficiency across the logistics mile.
Best Practices to Improve Your Inventory Receiving Processes
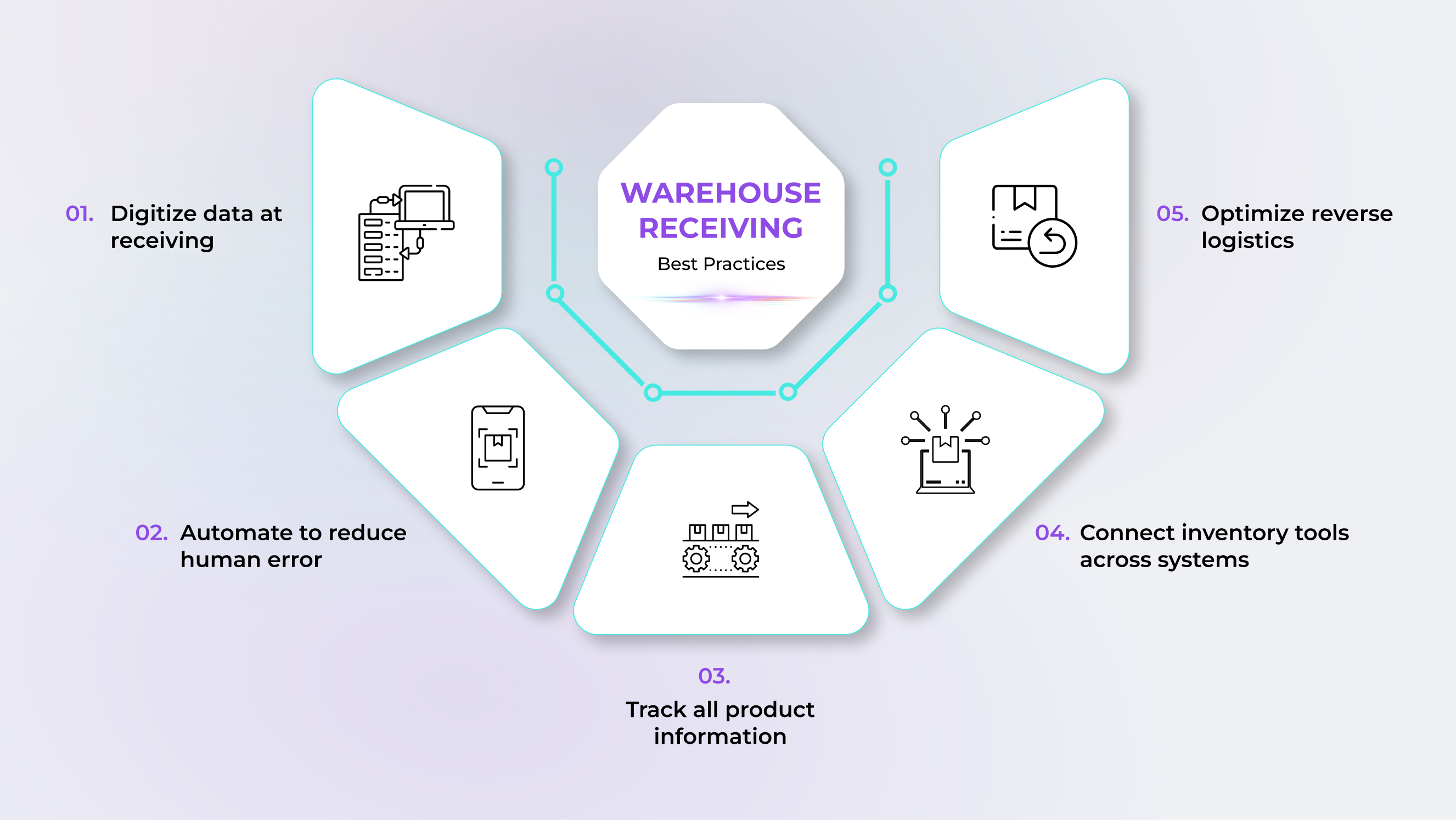
To truly optimize your warehouse receiving process, you need to follow best practices. By leveraging modern technologies, such as an inventory management system or a WMS, you can uplevel your warehouse receiving operations for better speed, efficiency, and accuracy. Below are a few must-follow best practices to help you get started.
Digitize data at receiving
Spreadsheets and paper-based data entry are prone to human errors. By replacing manual processes and digitizing data as goods are received, businesses can work with clean and standardized inbound data, which helps to improve data accuracy and improve inventory visibility and availability, leading to more informed decisions on how to optimize inventory and warehouse management.
Automate to reduce human error
Automating inventory receiving processes is not only great for reducing mistakes through human errors, it can also speed up operations and improve efficiency throughout the supply chain. Automated systems can be used for QR code and barcode scanning, data extraction from labels and BOL, data entry, and inventory verification, ultimately allowing for faster and more accurate demand forecasting and planning.
Track all product information
Downstream systems are only as good as the data they receive. When tracking inventory, or picking, packing, and shipping from a warehouse or fulfillment center, operators require highly enriched product information to improve inventory management and fulfillment operations.
Tracking all product information throughout the receiving process is essential. Using smartphones powered by OCR, QR code, barcode, and RFID technologies, businesses can extract detailed information such as SKU numbers, serial numbers, expiration dates, lot codes, and more. Comprehensive product tracking also helps with returns and reverse logistics operations as well.
Connect inventory tools across systems
Some of the issues with modern-day logistics operations include outdated legacy systems and siloed data sources that require heaps of custom code to integrate and communicate with each other. In a business like e-commerce, where even a slight delay could result in cart abandonment and lost sales, more inventory needs to be made available-to-promise to meet rising customer expectations. Furthermore, receiving, fulfillment, dispatch, and transfers are often disconnected across systems, creating inefficiencies and poor visibility across merchandising and fulfillment.
Today’s inventory management software should not only feature auto-capture of overages, shortages, damages, and returns, they should also integrate quickly and seamlessly with other business software. Modern, flexible, API-first solutions allow businesses to build their own logistics stacks that can connect inventory across an enterprise resource planning (ERP) system, WMS, accounting software, and more. Businesses can achieve faster time to value, eliminate data silos, reduce manual data entry, and improve decision-making across an organization.
Optimize reverse logistics
Another key aspect of the warehouse receiving process is reverse logistics, which involves handling returned or unsold goods. According to boutique research consulting firm Aberdeen Group, the expense for reverse logistics is around $100 billion each year in the U.S., making it essential for businesses to lower costs and improve efficiency.
However, instead of using disjointed systems to handle returns, a holistic logistics solution for inventory, fulfillment, and shipping that integrates seamlessly with other systems can simplify reverse logistics. Businesses can automate workflows with AI scanning systems, digitize the data, and make it accessible across an ERP, e-commerce platform, CRM, accounting software, customer support, and more. This allows businesses to process returns more efficiently, coordinate refunds, credits, or exchanges, communicate with customers, and restock items faster.
PackageX Optimizes Warehouse Receiving With Modern Tech
While every link in a company’s supply chain can be transformed into a durable competitive advantage, technology can make a huge difference by streamlining and automating warehouse-receiving processes.
PackageX empowers businesses to digitize their warehouse receiving operations through its suite of integrated apps and APIs. PackageX offers comprehensive solutions on a unified platform that enables users to streamline inventory and warehouse workflows, from powerful inventory management software for modern logistics to AI-powered scanning.
If you want to learn more about how PackageX can help you improve your warehouse receiving processes, we’d love to speak with you. Contact a team member or schedule a demo to experience how our modern platform can elevate your logistics systems today.
Warehouse Receiving FAQs
What are some metrics to track during warehouse receiving?
Key metrics to track during warehouse receiving include on-time delivery performance, receiving accuracy rate, inventory turnover time, and dock-to-stock time. These metrics help assess the efficiency and accuracy of the receiving process, identify areas for improvement, and ensure timely availability of inventory for downstream operations. Some additional warehouse storage KPIs include:
- Carrying cost of inventory: The cost of storing inventory over a period of time and some other costs.
- Storage productivity: This informs the volume of inventory stored per sq. ft.
- Space utilization: This is the percentage of the inventory space per total storage capacity.
- Inventory turnover: This informs the number of times an inventory was sold or replenished within a period of time.
- Inventory to scale-ratio: A metric that informs carrying inventory per sales.
What is pre-receiving in a warehouse?
Pre-receiving is a preparatory stage of the warehouse receiving process where businesses complete necessary tasks before receiving inventory. This includes establishing receiving requirements, preparing documentation, and coordinating logistics with suppliers or carriers. Pre-receiving ensures that inventory is received smoothly and accurately, minimizing delays and errors in the receiving process.
What is putaway in warehousing?
Putaway refers to the process of placing received goods into designated storage locations within the warehouse. It involves determining the optimal storage location based on product type, size, demand, and storage capacity. Putaway ensures efficient use of warehouse space, facilitates easy retrieval of inventory for order fulfillment, and contributes to overall warehouse organization and productivity.
What are the main steps in the receiving process?
The process of warehouse receiving involves several steps to accept, inspect, document, and store incoming inventory. The main steps in the receiving process typically include:
- Complete pre-receiving tasks
- Receive and unload goods
- Count and inspect inventory
- Organize and store inventory
The number of steps in the receiving process can vary depending on the specific procedures implemented by each warehouse.
What is the receiving procedure?
The receiving procedure refers to the set of steps and protocols followed by warehouses to accept and process incoming inventory. This typically includes steps such as inspecting received items, documenting the receipt of goods, allocating storage locations, and updating inventory records.